Once again, we find ourselves at The Place! Our subject for today’s meeting is a man famous in Cyprus not only for being a master of glass art but of course, like all my interviewees within these walls — a talented artist.
Andreas has invited us to his display hall. It’s filled with painted glassworks: from cute little trinkets and jewellery pieces to decorative dishes, panels, frames and other items, — the rays of the midday sun playfully shine over their smooth curves and technicolour surfaces.
Andreas tells us with great enthusiasm: Fusing [1] is the oldest technique of working with hot glass. So, any type of glasswork includes two specialities — a multitude of techniques involving hot and cold treatment. Fusing — as with Murano glass, glassblowing and moulding — concerns the “hot” technique. In fact, we have been aware of fusion glass since the times of Ancient Egypt (jewellery).
This is the finest of the hot glass techniques, and the most time-consuming at that — a large item (a panel, for example) will take you around two months to make! The principle is as follows: take a sheet of transparent glass — a substrate, coat it with a special adhesive and cover it with coloured glass [2], either which has been reduced into a “powder” or broken into pieces, then sinter it together.
After cooling, the finished project will be one single piece.
By the way, if the item hasn’t turned out as planned and you need to make it anew… it is simple to melt, with all its colours still preserved when melted.
As such, this “powder” is used in both fusing and glassblowing.
— Many people today are drawn to glass and the possibility of making something from it themselves, for example, at home…
— All the same, it’s better to use industrial kilns and equipment. Look, for instance, at the “cold” stage of treating glass, which initially requires you to “cut it open”, right? You’ll also need to polish the cut, — even here you’ll need to be an artisan of this craft with sufficient experience.
Thus the art of fusing “from and to (the finished product)” generally incorporates both treatment processes — hot and cold.
— I see that some of your most impressive works (vases, dishes and others) were created with multilayered glass, is that correct?
— Yes, there are some with six or more layers of glass, each of which has a thickness of 3 mm. Such things can take me up to 1.5-2 months of work: for each “approach” I create a coloured layer. If the item is intended to be multicoloured, with sophisticated effects, — each of the layers is done separately.
On the whole, the heating process takes up to 7 days. Then roughly another three days is required near completion, to let the item cool down.
— What if you do something wrong?
— Break it all and start again!
— The colours of the powdered glass: don’t they change when fused?
— The colours and their brightness are changeable: it all depends on the temperature of the kiln.
— Which type of glass is used for fusion works?
— When getting to work, of course, you need to determine which “material” to use: each glass has its own specific character and purpose. In this case, naturally, we use “float” glass for the substrate (a wide assortment of frits, rods and other similar items, are made using float glass).
— Do you use locally manufactured or imported glass?
— Cypriot manufactured glass (editor’s note: please see our article on glassware — the local manufacturers and their specialities are indicated).
— Is it true that most of the labour involved in creating large decorative items is carried out today by men in particular?
— Of course not, it works both ways: men and women do it.
— Andreas, who is your “target audience”: who takes the most interest in your art?
— It can be both Cypriots and foreigners, by and large, from Northern Europe.
But the Swiss and the Germans — they are adepts at this craft and well-versed in its methods, it’s the process and technique of my work — the nuances, in a word — which interest them.
— By the way, regarding techniques, what can you say about the famous Murano technique?
— Ha, funny thing, actually… there isn’t one. Surprised? In essence, you see, when making Murano, you use the same techniques which are, one way or another, present in glassmaking everywhere. Not only on the island of Murano.
This would roughly be like us saying “Mickey Mouse” instead of “animation”.
So, the Italian island, which uses these traditions, has simply “branded” them. In fact, “Murano” isn’t as much the perfect technique — better than any other — which it’s painted out to be. In practice, of course, it’s much more profitable to make and sell one of these so-called “Murano” vases, then buy a house with this money, than to be one of many simple craftsmen selling their works for far less.
— What a surprise, as the saying goes!
So what advice would you give to our readers? How do you choose a quality piece of glassware if you’ve just popped into one of the shops, or find yourself on а street market in one of the tourist regions? What should you pay attention to?
— Fused glass, for instance, is of practically the same quality everywhere. The main thing, for any piece of glassware, is that it must look harmonious from a visual perspective: it should have a definite shape, a smooth, shiny surface and an equal thickness to its walls (if it’s a vessel, let’s say).
Naturally, on high-quality, hand-made glass, you won’t find any seams to it; the bubbles inside, on the other hand, are another way to confirm whether you’ve made the correct choice, as you can immediately see: this was made…properly, by hand.
— Is fused glass suitable for manufacturing any decorative item? What do people most often order from you?
— Yes, you can use practically any type… but, as we’ve already said: for every item — there’s the right piece of glass!
In my workshop, for example (Athenas Street, 20A; Paphos), I produce rather large works: panels, plafond ceiling installations, mirror frames, tabletops and sinks.
A glass sink, let’s say, made to order for a bathroom, will be 15 mm thick.
— It looks amazing… but how do you shape it?
— So, we first make the necessary measurements. We add coloured glass based on the customer’s wishes and then choose the appropriate shape — the model is a ceramic or stainless-steel sink.
We place down, let’s say, a tester piece of glass, for preliminary fitting. We obtain a shape from it, then work with the primary material.
Thus we use the moulding technique of “bending” the glass. In the kiln, on top of the model [3], we place a divider and sheets of glass “with spares”… sometimes up to seven layers. We then heat the glass, and it acquires the intended shape, which we can work with further. Afterwards, it’s all straightforward: we cool the glass, take it out, treat the edges and then drill a hole for the drain and tap (if the item has a tabletop). Your sink is ready!
We also use special fire-resistant (furnace) bricks: the glass remains on the module with the applied ceramic powder — and we work by hand.
You can always create various additional decorative effects, such as sculptural (like fabric, you can add folds, decorative details etc.) or metallic inclusions (copper and brass sintering, metallic powders, gold, platinum).
Craftsmen never know what the exact result will be and based on what comes out, they have to decide what is worth adding or altering.
Due to the large amount of labour invested, the lengthy manufacturing process and this being a rather arduous, creative endeavour, — if you want a ready-made, signature fusion sink, with artistic effects, today it will cost close to two thousand euro.
If somebody says to me: “How amazing! I want the same”. Well, we take the model’s shape, heat it up, — and the process is repeated. After manufacture of a large glass object, the model from the tester glass is smashed and can later be recast to create a new sample for future items.
Want to see something funny? Here’s one of my “testers” — this draft piece turned out to be undersized — it had stayed in the kiln for a little too long. And what do you know, with just a “flick of the hand” it turned into an original vase!
— In general, if you need to make an item from a “botched” piece …
— We break up the old mould — its new colour remains unchanged (if you don’t include other colours, of course) — and we throw in as much glass as is necessary for the future vase. We melt everything until a single mass has formed, after which we lay its shape.
If your readers are interested in seeing how I work, they can visit my site www.nemeaco.com; I can’t invite people to my workshop, as you need special glasses to look at scorching hot glass, and glassmakers themselves have to wear a mask to avoid inhaling the fumes.
Here’s another method of glasswork, one which will imitate the work of basket weavers — shall we find out more? These dishes may seem woven, but they’re actually made by slicing glass into rather thin strips — you have to first make an outline, of course — then lain into a criss-cross shape. No glass “weaving” is required — simply heat it all together, and you may add specks of colour if you wish.
You see, this common effect is achieved here in a different manner.
Of course, I produce all my glassworks myself in my workshop, while here — at The Place — I sell ready-made items, I interact with customers and tourists.
— A practical question: do you take on apprentices?
— I don’t take any apprentices on whatsoever, too much effort already goes into my main work!
Nowadays, in my craft (I have been working with glass as a professional for around 10 years), I get help from my brother, who finished his studies in England. I moved to Athens in 1999, where I underwent my training; and then I spent the following years in Russia (Moscow) — where I completed my training and made considerable progress. Although a true master never stops building experience. They gain more knowledge about the nuances of their trade. This truly is an endless process!
I returned to Cyprus in 2008 and opened my own studio for creating fusion art. My brand, Nemea — which dates back to the year 2009 — specialises in interior design and architecture (ceiling installations, wall panels and a variety of smaller decor items).
-
Editor’s note: to find out where to learn the art of fusing in Cyprus, please see our previous article. Andreas says that the local masters taking on apprentices live mainly in Larnaca.
-
I wish that all novices to this trade find themselves an excellent teacher and practise with silica sand…I also began with this: place it into a kiln and start to try shaping it once it has melted.
We thank Andreas for his time and an interesting interview
Stay with us and until next time!
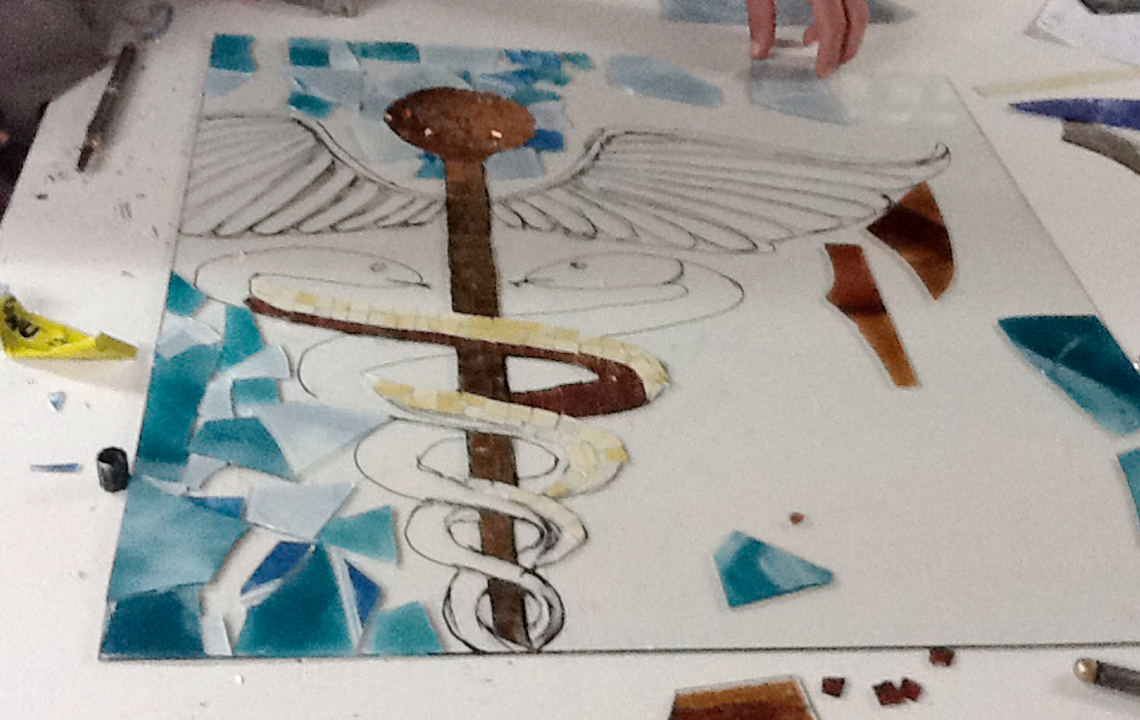
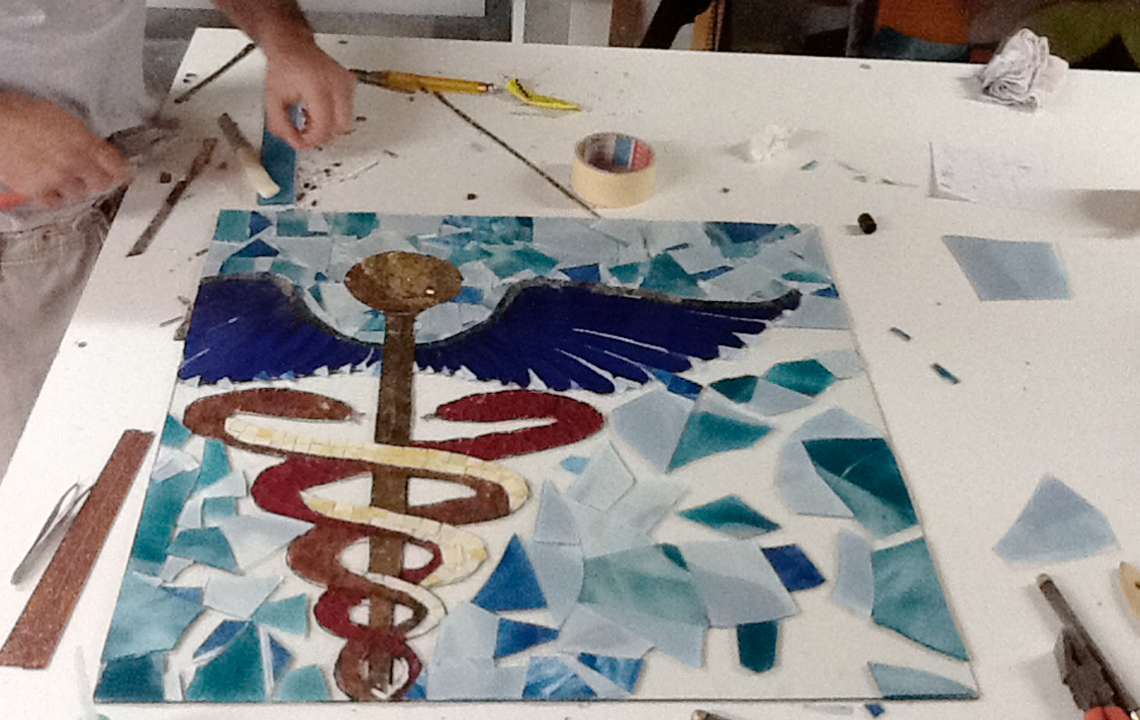
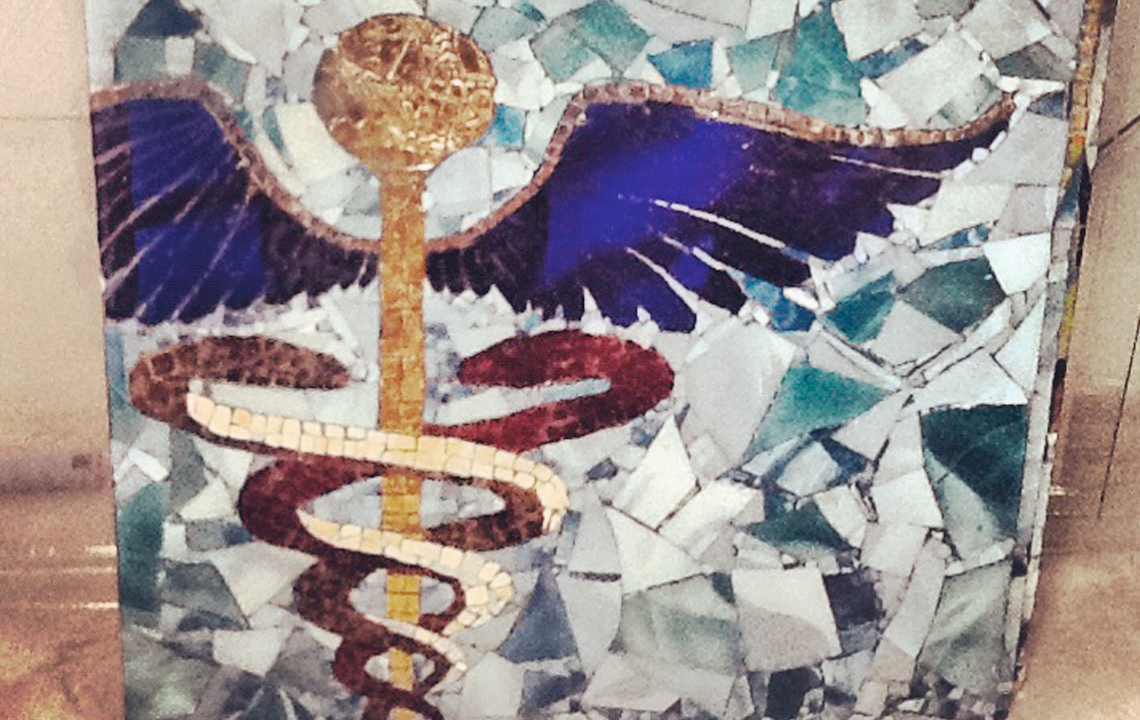
[1] The technique, known to us today as “fusing”, is essentially an original alternative to an age-old method of heating enamel. The use of a metallic plate here is no longer required, as the base is made of glass.
[2] The kiln dyes are split into transparent and opaque sorts with enamel inclusions.
[3] Multi-use ceramic and steel (metal) shapes are used for manufacturing sizeable glass objects: plates, dishes, vases etc. Metal shapes formed from them are most often used for moulding (bending glass). Aside from bending, metal is used to obtain glassware with a glossy and even back surface.
But to give the item a complex shape, various materials are used: plaster, concrete and soft slabs.